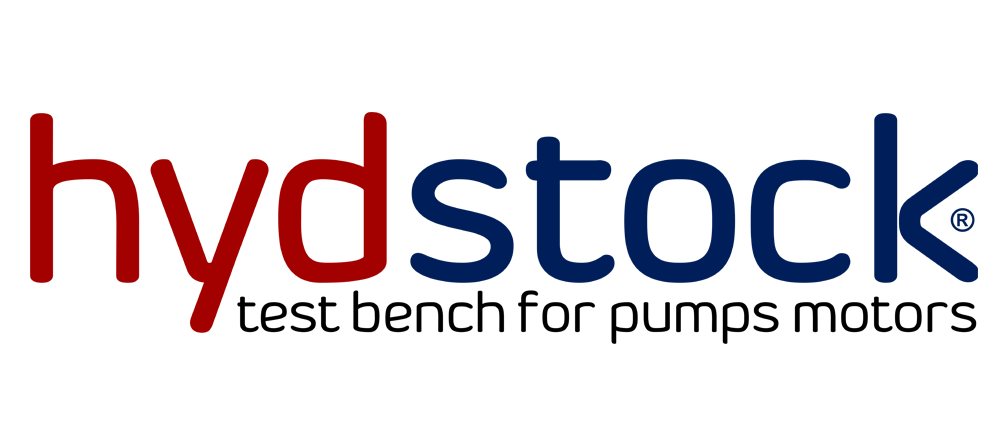
Our Test Bench's used on the Bent Axis Piston Pumps, Hydraulic Piston Motors, Variable Displacement Piston Pumps and Hydraulic Gear Pumps.
An orbital-style motor consists of several roller vanes positioned in pockets around the inside diameter of a stator, that act as a guide for an internal rotor to orbit. The rotor’s rotation is achieved through a pressure differential created by fluid flow. Constantly shifting high- and low-pressure zones are created, resulting in a smooth and consistent rotation. Once the fluid has moved through the motor, the fluid can be returned to a holding tank, or directly to the pump itself. The rotor drives an output shaft, which is connected via a “dogbone”-style drive link. This output shaft is connected to whatever is being driven (a wheel, auger, conveyor, etc.), and high torque can be applied. This direct connection creates a smooth transfer of the required speed and torque for an application. There are two, smaller groups of low-speed, high-torque orbital motors, two-zone and three-zone. The primary difference between a two-zone and three-zone motor is the inclusion of a case-drain. A three-zone motor uses a case drain as a secondary outlet, where fluid can be returned to a tank (or pump) if the application’s pressure becomes too high. Alleviating this pressure aids cooling and can extend motor seal life. Additionally, the case drain line can drain excess internal oil leakage. This design feature allows three-zone motors to be linked in series for higher-pressure applications while maintaining the flow levels of a two-zone torqmotor. In the case of a two-zone motor, the absence of a case drain means that extra adapters and hoses are not needed to connect a secondary outlet, making the entire system more cost-effective. Two-zone motors can be equipped with high-pressure shaft seals to bolster capability, but can not perform in the same, high-pressure environments as a three-zone motor.
_
_